In today’s FDA-regulated life sciences sector, where quality and compliance are not merely objectives but imperatives, robust quality planning should be a foundational activity to achieve a sustainable risk balance for sustainable quality and compliance outcomes.
Given this, it is surprising to see from our work with clients that sometimes even the best, well-established companies have not embraced a regular, strategic, and tactically-driven approach to quality planning.
Compliance Architects regularly advises clients that a strategic, anticipatory approach to quality planning mitigates potential risks, bolsters operational efficiency, and reduces costs — all outcomes that are necessary for regulated companies to flourish within today’s complex regulatory landscape.
Table of Contents
Addressing Modern Quality Challenges
Organizations today grapple with many challenges that impede sustainable quality and compliance outcomes. Challenges include, but certainly aren’t limited to obsolete documentation practices (including poorly drafted and unfriendly standard operating procedures (SOPs)); inflexible and poorly designed global change control processes;
insufficient science driving process controls; lack of oversight on and integration with external supply chain providers; regulation overload; competence and training deficiencies; and many more.
A pervasive issue exacerbating these challenges is the disconnect between quality planning and organizational imperatives, often resulting in disjointed compliance initiatives that fall short of fulfilling long-term strategic goals. Effective quality planning requires a firm linkage to short-, medium-, and long-term business plans and overall corporate intent on assumptions of risk, necessary profitability, and measures of financial success.
To overcome these foundational issues, quality planning must extend beyond merely addressing immediate compliance needs and be derived from and consistent with overarching operational objectives.
Critically important to support vital quality planning, organizations need to cultivate a quality culture that aligns with organizational intent. An organization’s quality culture must be supportive of quality planning activities such that all aspects of the organization are “pulling on the oars” in sync. Without this alignment, embracing a strategic approach to quality planning becomes difficult at best.
The “Winchester House of Quality” – Evolution and Happenstance vs. Design Intent
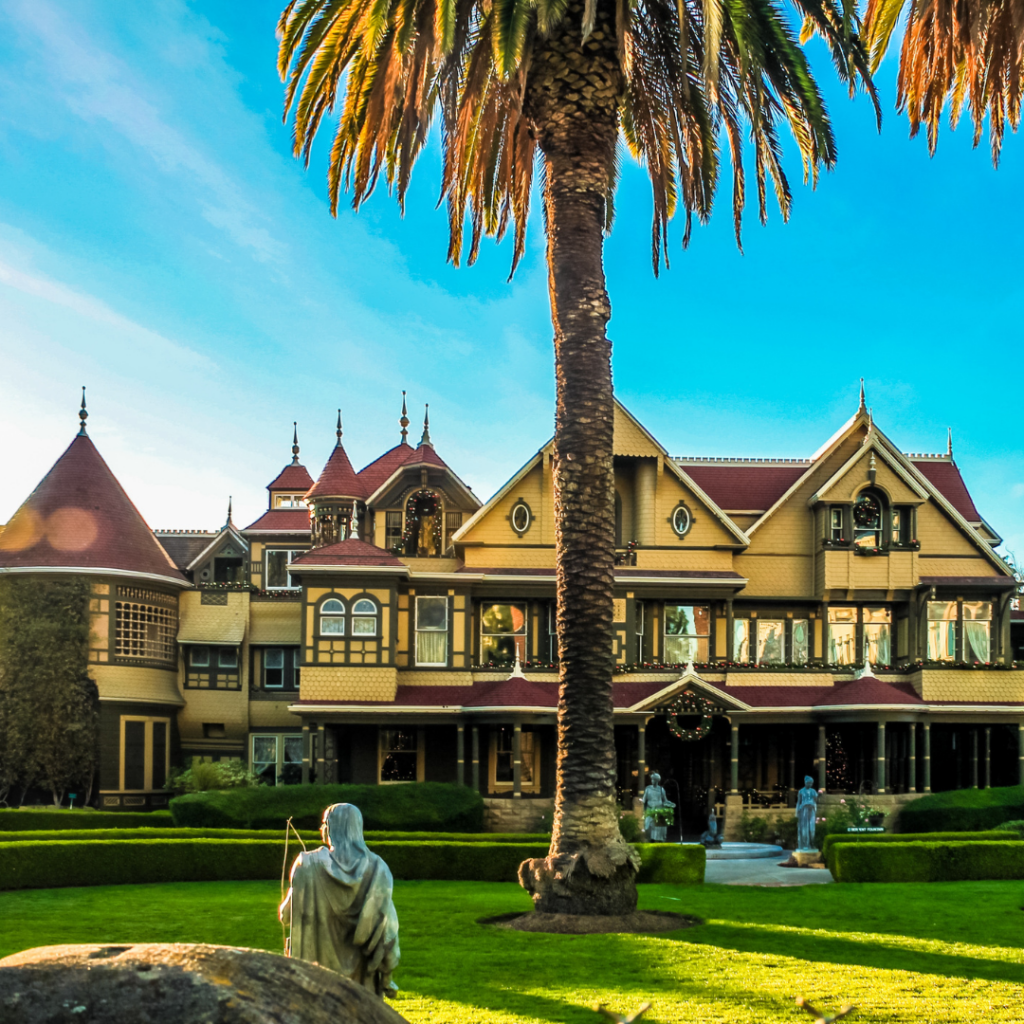
The hazards of unplanned, reactive, action-oriented changes to a regulated life science manufacturer’s quality system and supply chain operations can be likened to what we call the “Winchester House of Quality.”
Like the famous, perpetually incomplete mansion, quality and operational systems often develop reactively and haphazardly, creating disconnected systems, inconsistent approaches, poorly designed processes, and lacking the integration and consistency essential for sustainable quality, compliance, and supply-chain outcomes.
This disintegrated (but far too typical) approach to problem resolution and growth leads to disparate standards, unclear responsibilities, and fragmented quality and compliance mechanisms.
To address this natural tendency towards disorder (entropy, anyone?), companies must periodically re-architect their quality systems to align with their current business model, business intent, product portfolios, and inherent operational capabilities.
To achieve this, envisioning an “end state” for quality systems is crucial, and developing a coherent, efficient, and well-integrated framework to support global and local compliance demands is an important part of this activity.
Establishing a cohesive, enduring quality infrastructure transcends merely adhering to regulatory standards; it involves embedding efficiency and risk cognizance at every organizational tier.
Crafting a Well-Architected, Risk-Balanced Quality System
A practical quality planning approach starts with defining and visualizing the end state. Companies need to understand their strategic goals, objectives, intent, and operating realities to establish a well-designed, understandable, well-controlled, resilient quality system capable of navigating regulatory uncertainty, managing risks, and adapting to market dynamics.
Compliance Architects suggests incorporating the following elements when designing your future-state, business-aligned, durable quality system:
- Global Compliance Governance: Develop a framework that facilitates coordination across regions, countries, or locations while accommodating flexibility for local market requirements.
- Science-Based Decision-Making: Infuse science and robust data and analytics into quality management processes, ensuring quality is not just a compliance metric but a strategic business asset.
- Change Control & Risk Management: Implement a structured change control process that manages global and local changes, focusing on risk prioritization.
- Executive Leadership & Governance: Strong executive involvement and well-defined governance structures foster accountability and cultivate a proactive quality management culture.
Embedding these foundational components within a quality system enables organizations to manage quality from both strategic and tactical perspectives, balancing risk management with operational imperatives.
Shaping the Future Through Quality Planning
Crafting a strategic quality roadmap requires more than merely addressing compliance issues—it necessitates a fundamental shift within the organizational mindset.
Companies need to slow down and plan. Focus and prioritization must be incorporated into plan development. Leadership is pivotal in nurturing a culture where quality is perceived as integral to operational success. Compliance Architects advises that forward-looking quality planning include (but not be limited to) the following:
- Clear Vision & Prioritization: Formulate a strategic, realistic, pragmatic and doable quality and compliance vision that delineates long-term quality objectives, addresses current deficiencies, and aligns with organizational goals.
- Structured Roadmap Development: Identify actionable projects and milestones that pave the way toward the desired future state. This phased approach ensures alignment and smooth integration with ongoing operations.
- Rigorous Execution for Projects and Initiatives: Obtain expert assistance with project management and execution that are outside of base business activities. Ensure executive incentives are aligned with projects’ success and long-term outcomes.
- Regular Evaluation & Adaptation: Continuously and periodically evaluate the progress of quality initiatives, refine strategies as needed, and address emerging risks.
Strategic quality planning transforms quality from a static requirement into a dynamic driver of organizational success.
By setting clear objectives, implementing structured processes, and engaging in ongoing evaluation, companies can attain sustainable quality operations that comply with regulatory expectations and enhance business performance.
Realizing the Vision: Ensuring Enduring Impact
A pivotal aspect of executing an effective quality strategy is translating the vision into practical, everyday actions. This entails empowering personnel with the requisite skills and knowledge to uphold quality standards, fostering transparency in decision-making, and maintaining a focus on quality across all organizational levels.
As initiatives progress, organizations should monitor performance metrics, validate impact, and refine approaches to ensure continuous alignment with risk management goals and organizational objectives.
Elevate Your Quality Planning with the CRPN Quality Roadmap®
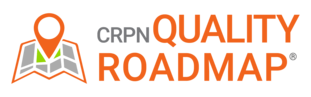
To take your quality planning to the next level, consider the CRPN Quality Roadmap®—an innovative service solution from Compliance Architects designed to help regulated life sciences companies prioritize quality and compliance risk (and consider complexity) as part of broader quality planning activities.
The CRPN Quality Roadmap® is a service solution that combines a structured methodology, proprietary risk and complexity algorithms, and sophisticated reporting capabilities to facilitate intelligent, risk-based planning.
With it, companies can assess and prioritize risks, create efficient remediation plans, and align quality initiatives with organizational goals.
Trusted by leading organizations worldwide, the CRPN Quality Roadmap® empowers companies to approach complex quality challenges pragmatically and effectively.
Discover more: Download our free introductory deck here, explore a real-world case study, or watch a joint presentation with Bayer’s VP of Quality to see how the CRPN Quality Roadmap® can transform quality planning into a strategic advantage.
In conclusion, quality planning is necessary for all FDA-regulated life science companies to establish a sustainable, risk-conscious foundation for long-term success.
By committing to strategic quality planning, life sciences organizations can more adeptly navigate regulatory challenges, optimize operational performance, and position themselves for a robust future.
Frequently Asked Questions (FAQs)
How can I start building a Quality Plan for 2025?
Begin by understanding organizational goals, and by setting clear quality goals that align with your organizational objectives. Our expert consultants and service offerings like the CRPN Quality Roadmap®, can help you create a robust plan from day one.
Why is quality planning so crucial to risk management?
A proactive quality plan helps you identify, prioritize and mitigate risks before they impact operations, making it easier to maintain compliance while optimizing efficiency.
What are some common challenges in quality management for life sciences?
Key challenges include outdated documentation practices, inconsistent global change control, lack of integrated communication channels, and insufficient science-based decision-making.
These issues can create a disjointed quality system that fails to meet long-term needs, often resulting in isolated areas of compliance rather than a cohesive, efficient quality management system.
How can an organization develop a cohesive quality management vision?
Developing a cohesive vision involves visualizing and defining a desired “end state” for quality systems. This includes ensuring a globally aligned compliance governance structure, embedding science into decision-making processes, implementing structured change control, and fostering executive leadership that promotes accountability and a proactive quality culture.
How can organizations ensure continuous improvement in their quality systems?
Continuous improvement requires regular assessment of quality initiatives, possible re-alignment of internal system changes, and refinement of strategies as organizational needs and industry standards evolve.
Organizations can adapt their quality systems to sustain regulatory compliance and operational effectiveness by tracking performance metrics and fostering open communication.
Can I get personal support on quality planning from Compliance Architects?
Absolutely! Reach out today to obtain specific guidance or to discuss how we can help tailor a quality plan for your organization. We can also help you understand your quality culture with industry’s only purpose-built quality culture diagnostic, Quality Pulse®.
What role does Compliance Architects play in quality planning for life sciences companies?
Compliance Architects specializes in developing sustainable, risk-focused strategic quality frameworks. Through services such as quality system design, compliance governance, and risk management, They help life sciences organizations navigate regulatory landscapes, optimize quality processes, and achieve operational resilience.
Do you want to take the first step toward improving your organization’s quality and compliance outcomes? We’d love to have a conversation with you about quality planning. Contact us below to speak with one of our quality planning experts.